The use of rubber gasket seal strips in various industries underscores their indispensable role in ensuring effective sealing solutions. As a seasoned expert in gasket technology, it's crucial to delve into the intricate details and verify the superiority of rubber gasket seal strips in diverse applications, ranging from automotive to industrial machinery.
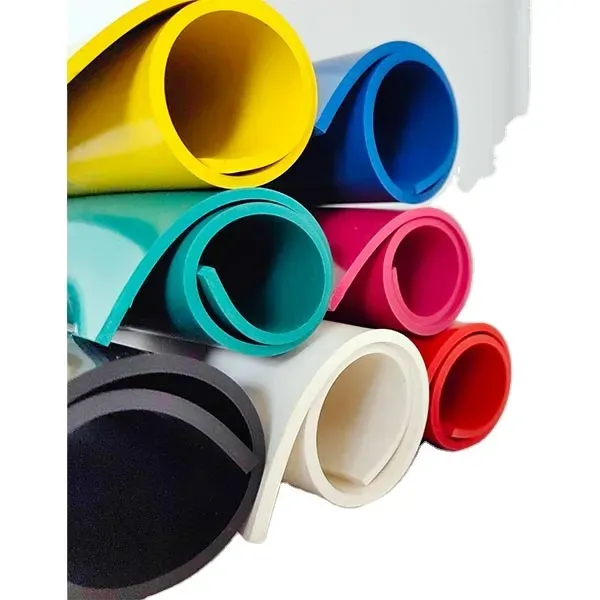
The appeal of rubber gasket seal strips is primarily due to their unrivaled ability to create a leak-proof seal between two surfaces. Constructed from durable and flexible materials, these strips are engineered to withstand the pressures of complex systems, offering exceptional resilience against heat, pressure, and chemical exposure. This makes them particularly valuable in automotive industries where they must perform under strenuous conditions, ensuring the safety and efficiency of vehicles.
In industrial machinery,
the importance of gasket seal strips cannot be understated. They play a critical role in maintaining operational integrity by preventing leakage of fluids, thus ensuring the machines function smoothly and reducing the risk of expensive downtimes. The selection of appropriate rubber gasket materials can impact a company's bottom line significantly by minimizing maintenance costs and enhancing equipment longevity.
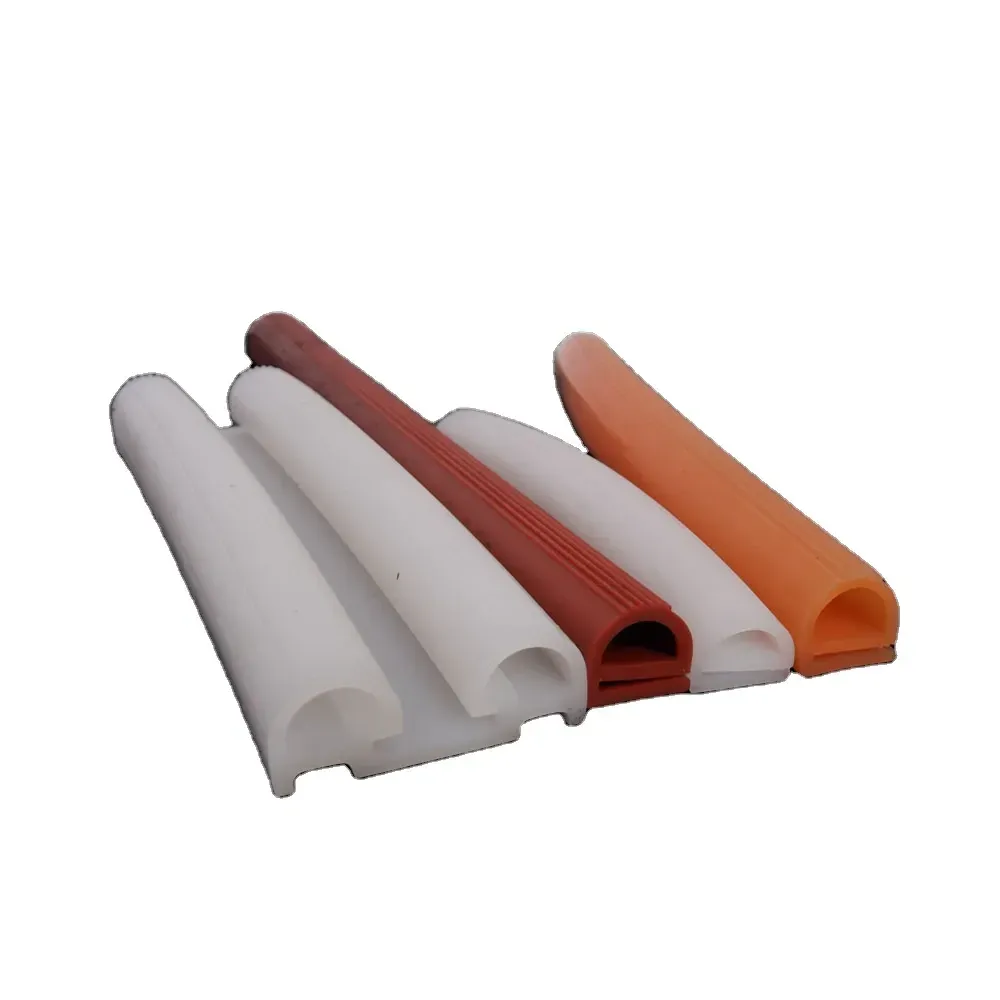
When discussing the versatility of rubber gasket seal strips, one must consider the broad spectrum of materials available. For instance, EPDM rubber gaskets are renowned for their exceptional weather and ozone resistance, making them a preferred choice for outdoor applications. Nitrile rubber is often employed in situations requiring oil resistance, while silicone rubber is sought after for high-temperature applications due to its thermal stability. Understanding the material properties is pivotal for selecting the right gasket for specific needs, a decision that demands both expertise and foresight.
Moreover, the design and production process of rubber gasket seal strips incorporate advanced technologies to ensure precision and reliability. Computer-aided design (CAD) systems allow for meticulous specification of dimensions and shapes, ensuring that each gasket adheres precisely to the equipment or surface requirements. This technological approach not only enhances the performance of the seal strips but also instills confidence that they will perform their intended function without fail.
rubber gasket seal strip
The authoritative nature of rubber gasket seal strips is further reinforced through rigorous testing and certification processes. Reputable manufacturers subject their products to stringent quality control measures to ensure they meet or exceed industry standards such as ASTM, SAE International, or ISO certifications. These standards are benchmarks of reliability, serving to enhance trustworthiness and ensuring that companies and consumers alike can rely on the products under various operational conditions.
Real-life experiences from industries utilizing rubber gasket seal strips are testament to their efficacy. For example, in the automotive sector, rubber gaskets are instrumental in enhancing fuel efficiency and reducing emissions by preventing leaks that could compromise engine performance. In manufacturing plants, the application of these gaskets in machinery ensures operational continuity, thereby elevating productivity rates and minimizing unforeseen downtimes, a critical factor in competitive industrial environments.
The longevity and sustainability aspects of rubber gasket seal strips also merit consideration. Rubber gaskets, if appropriately maintained, can offer extended service life, reducing the frequency of replacements and contributing to the sustainability goals of industries. This is particularly relevant as companies globally strive to implement environmentally responsible practices, thereby reinforcing the relevance of durable and efficient sealing solutions.
In conclusion, the multifaceted applications and benefits of rubber gasket seal strips exemplify their integral role in modern industries. The combination of specialized materials, advanced production techniques, and rigorous testing positions these gaskets as reliable and authoritative solutions. Their proven performance across various sectors not only underscores their indispensability but also cements their status as a trusted component in achieving operational efficiency and reliability. The expertise required to select and employ the correct gasket further enhances their value, ensuring that they remain an essential part of industry-standard sealing technology.