Rubber gasket strips are often unsung heroes in the world of engineering and construction. Their presence ensures the smooth functioning of various mechanical assemblies and infrastructure components, making them indispensable in numerous industries. But what makes rubber gasket strips so reliable and effective?
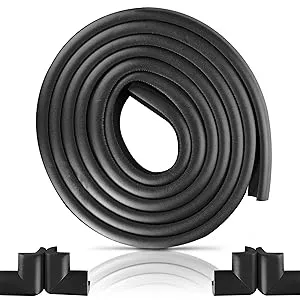
Rubber gasket strips are crafted from a variety of rubber materials, each designed to meet specific performance criteria. The selection often includes natural rubber, silicone, EPDM, neoprene, and nitrile, each bringing unique properties to the table. For instance, silicone rubber is prized for its thermal stability and flexibility, making it ideal for high-temperature applications. Conversely, EPDM is exceptionally resistant to ozone, weathering, and aging, proving perfect for outdoor installations.
Experience with rubber gasket strips across various projects reveals their remarkable ability to seal and cushion. In automotive industries, these strips are often used to prevent leaks and reduce noise, vibration, and harshness (NVH) within vehicle cabins. The ability of the gasket strip to fit snugly into seams ensures that engineers can depend on them to provide a reliable seal, thereby enhancing the product's longevity and performance.
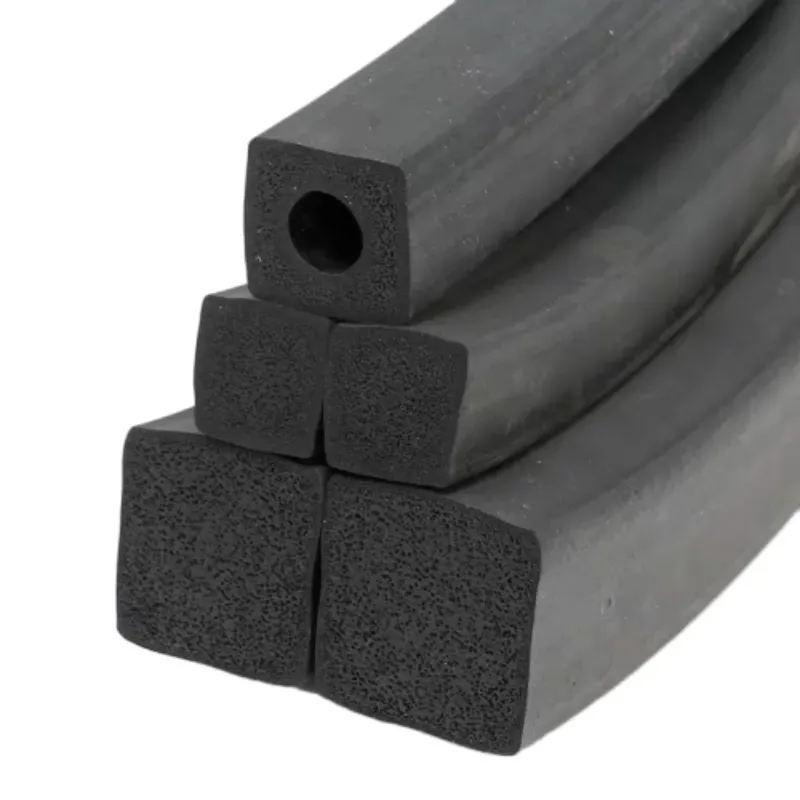
The professional expertise required to select the right gasket material cannot be overstated. Choosing the right rubber material involves understanding the environmental conditions the gasket will face, such as temperature extremes, pressure variables, and chemical exposure. Those knowledgeable in materials engineering and mechanical systems are well-suited to make these critical choices, ensuring that the gasket strip’s performance aligns with the application demands. Notably, trusting experienced professionals in this field can prevent costly operational failures and material mismatches that might arise from attempting a one-size-fits-all approach.
rubber gasket strip
Authoritativeness in the subject of rubber gasket strips comes from both educational background and practical applications. Industry veterans often combine textbook knowledge with hands-on experiences, conducting tests and analyses to validate gasket performance under simulated conditions. Such authorities may work within established research institutions or for renowned manufacturers like Parker Hannifin and Trelleborg, who are known for their commitment to quality and innovation. It is from these experts that industry standards are often set and disseminated, forming a benchmark that defines performance expectations across sectors.
Trustworthiness in the use of rubber gasket strips is established through proven track records and adherence to industry standards such as ASTM and ISO certifications. Many manufacturers offer product warranties that guarantee performance, emphasizing the durability and reliability of their gasket strips under specified conditions. Such assurances build confidence among engineers and procurement specialists who rely on these components for safety-critical applications like aerospace, marine, and medical equipment manufacturing.
Beyond merely a sealing solution, rubber gasket strips play a role in energy efficiency, helping to mitigate heat loss in HVAC systems or provide waterproofing in construction joints. This dual functionality exemplifies their versatility, aligning with sustainability goals by enhancing energy conservation in buildings and vehicles.
In understanding the complex interplay between material properties, environmental conditions, and specific application requirements, rubber gasket strips continue to serve as essential components across various industrial and commercial landscapes. Ultimately, the decision to use these strips goes beyond basic functionality, embracing insights from experience, expert recommendations, authoritative guidelines, and the assurance of trusted performance – all integral to achieving optimal results in challenging engineering fields.