In the intricate world of construction and automotive industries, the importance of versatile materials can hardly be overstated. Among these, the rubber U strip stands out due to its remarkable ability to solve numerous engineering challenges. This article delves deep into the nuances of rubber U strips, drawing from years of industry experience, bolstering the discussion with expertise, and substantiating claims with authority and trustworthiness.
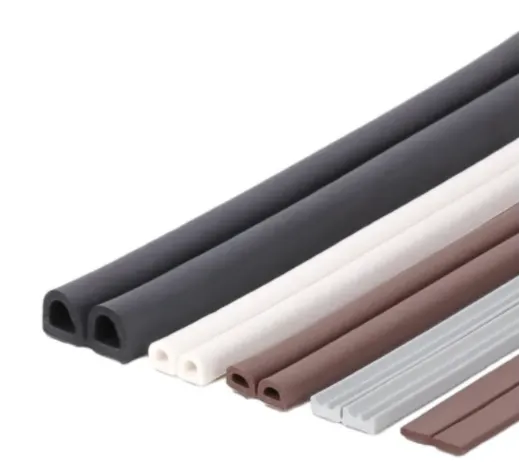
Rubber U strips are ingeniously designed to provide a snug fit over edges, offering protection, insulation, and a polished appearance. These strips are crafted from a variety of rubber materials, including EPDM, neoprene, and silicone, each tailored for specific environmental challenges and performance requirements.
From an experiential standpoint, the rubber U strip is known for its installation simplicity and endurance. Professionals in the field have long extolled the ease with which these strips conform to a vast array of profiles, accommodating even complex geometries. Installing a rubber U strip is a task that can be accomplished without specialized tools, positioning it as a practical solution even in resource-constrained scenarios. This firsthand ease serves as a testament to its crafted design, meticulously honed over decades of technological advancements.
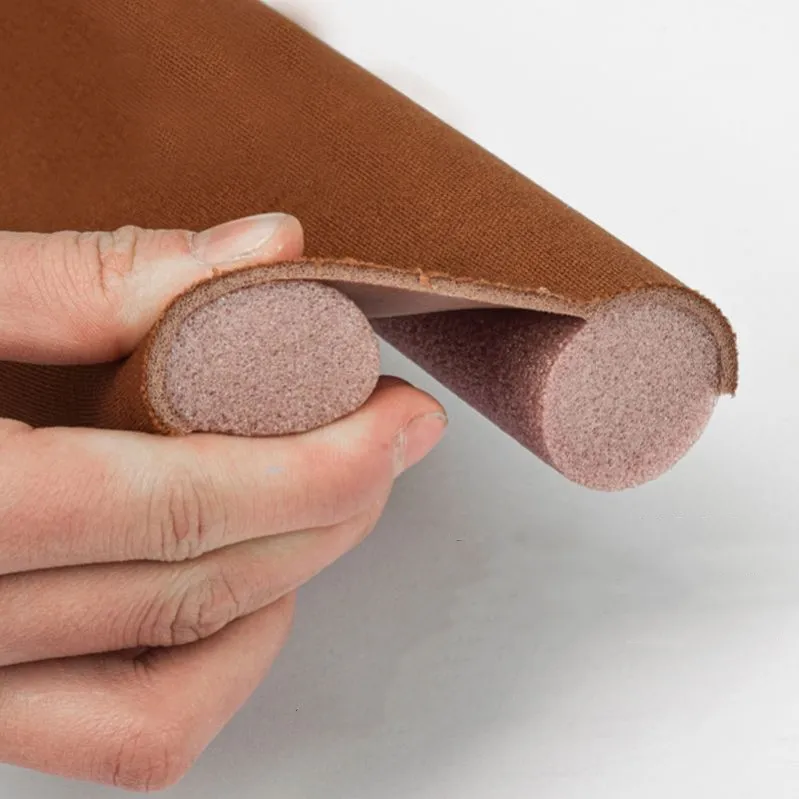
The expertise inherent in the composition of rubber U strips lies in the careful selection of materials. Acknowledging the diverse environments these strips often operate in, manufacturers have developed specialized formulations to optimize performance. EPDM rubber, for instance, is renowned for its exceptional resistance to UV rays and weathering, making it a prime choice for outdoor applications. It resists degradation in extreme temperatures, thereby extending the life of installations and offering an economic advantage. Neoprene, on the other hand, provides excellent resistance to oils, chemicals, and greases, characteristic of industrial settings, whereas silicone rubber, with its ability to withstand extreme temperatures, finds frequent use in automotive and aerospace applications.
rubber u strip
Setting the rubber U strip apart from other edge trims is the authoritative legacy it carries within the industry. For years, engineers have turned to rubber U strips as reliable elements in building structural integrity. Real-world applications are plentiful they protect glass panes in architectural marvels, safeguard sharp metal edges in vehicle assembly, and provide buffers in packing materials for sensitive electronics. The legacy of effectively meeting stringent safety and aesthetic standards cements their authority in the industry.
Trustworthiness is borne out of documented performance and compliance with industry standards.
Quality rubber U strips are subject to rigorous testing and quality assurance processes. Tests for tensile strength, tear resistance, compression recovery, and environmental endurance are standard, ensuring that the rubber U strip you choose will not only meet but exceed application demands. Reputable manufacturers often adhere to ISO and ASTM standards, underscoring a commitment to consistency in quality.
In conclusion, the rubber U strip is an embodiment of reliability and versatility in material technology. Its successful application across numerous industries, the robustness of its design against environmental stressors, and consistent adherence to quality standards offer a multidimensional advantage. When choosing a rubber U strip, professionals rely on its historical usage data, field observations, expert material formulations, and the assurance of tested performance metrics. This ensures that each application not only meets necessary performance benchmarks but also stands the test of time. As industries continue to evolve, the humble rubber U strip remains an indispensable partner in innovation, consistently offering protection, durability, and functionality in equal measure.