Rubber gasket door seals may not grab your attention at first sight, but they play an indispensable role in various industries, safeguarding environments and maintaining optimal operating conditions. Born out of necessity to ensure airtight and water-tight closures, these seals are often unsung heroes in technology and industry.
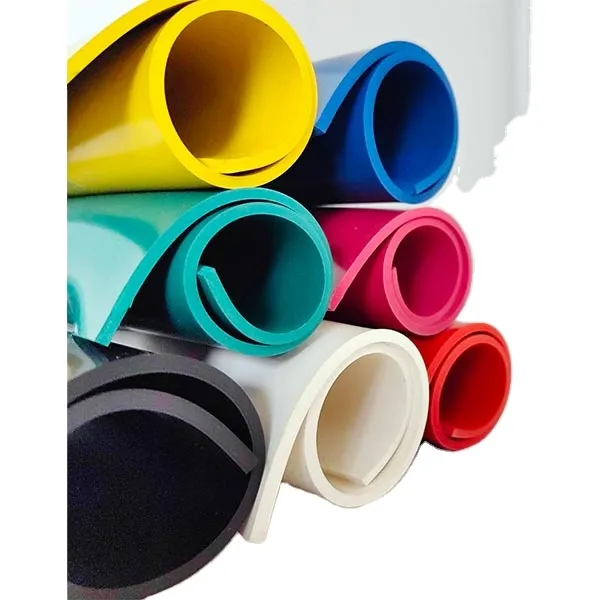
Imagine entering a room where temperature control is critical, such as a refrigeration unit. The door seal's invisible barrier is essential for maintaining internal conditions while keeping the energy consumption efficient. However, the functionality of these rubber gaskets transcends mere temperature control. They also play a pivotal role in protecting sensitive environments from contaminants and helping machinery operate smoothly over its lifecycle without recurring maintenance.
The science behind rubber gasket door seals is fascinating. These components are precisely designed to address specific challenges such as pressure differences, environmental exposure, and mechanical constraints. They are typically crafted from high-quality, flexible materials like EPDM, silicone, or NBR, each chosen for its resilience and suitability for different scenarios. Take, for instance, EPDM rubber, which is known for its excellent weather and ozone resistance, making it ideal for outdoor applications. Silicone, on the other hand, is often selected for its thermal stability and non-reactivity, suitable for high-temperature scenarios.

Professionals in industries like automotive manufacturing and aerospace often weigh the benefits of custom vs. standard rubber gasket door seals. Custom seals offer tailored solutions to fit unique applications and requirements, ensuring the highest level of efficiency and protection. Meanwhile, standard seals might suffice for conventional needs and provide a cost-effective and readily available option. The decision hinges on a delicate balance between performance needs and budget considerations, a dance familiar to engineers and supply chain managers.
An interesting development in the world of rubber gasket door seals is the focus on sustainability. As industries recognize the environmental impact of synthetic materials, there is a growing demand for seals produced with eco-friendly processes and materials. Recycled rubber, alternative natural materials, and innovative designs focused on reducing material waste are increasingly making their way into mainstream applications. As these materials are refined and optimized, they promise to deliver excellent performance with minimal environmental footprint, a win-win scenario for both producers and consumers.
rubber gasket door seal
It is important to consider the expertise required for the proper installation of these gaskets. A misaligned or improperly fitted seal can significantly compromise an entire system's integrity, leading to leaks, energy waste, and potential product spoilage. Thus, enlisting skilled technicians is not a luxury but a necessity to ensure that the seals deliver their maximum potential benefits. Training programs focusing on installation and maintenance are pivotal in ensuring long-term functionality and optimal performance.
Rubber gasket door seals, when maintained correctly, often have impressive lifespans. However, maintenance should not be neglected, as accumulated wear from constant use can eventually lead to failure. Regular checks for signs of cracks, stiffness, or visible damage should be a part of routine maintenance plans. Replacing worn gaskets promptly is crucial to avoid larger systemic failures and maintain operational efficiency.
In conclusion, rubber gasket door seals might appear mundane, yet they embody a remarkable confluence of engineering precision, material science, and practical application. As advancements in material research and sustainability continue to evolve, these components will undoubtedly become even more critical to industrial processes worldwide.
Choosing the right rubber gasket door seal necessitates a comprehensive understanding of your specific application requirements, environmental conditions, and operational demands. Collaboration with experienced producers who prioritize quality ensures your systems remain sealed, safe, and efficient, supporting both economic and ecological goals. As the unsung protectors of system integrity, these seals deserve recognition for their quiet yet critical service across myriad applications.